Rotary Printing Press
Rotary printing is an important process in the printing industry. The technique is used in many fields, such as label-making, textile printing, and printing money. This printing method has been around for over a century and goes by three different terms. They are direct cylinder printing, direct-to-object printing, and cylindrical printing.
In rotary printing, a rotating cylinder transfers ink onto a cylindrical surface. This results in intricate and repeatable designs on items like candles, cups, and dishware.
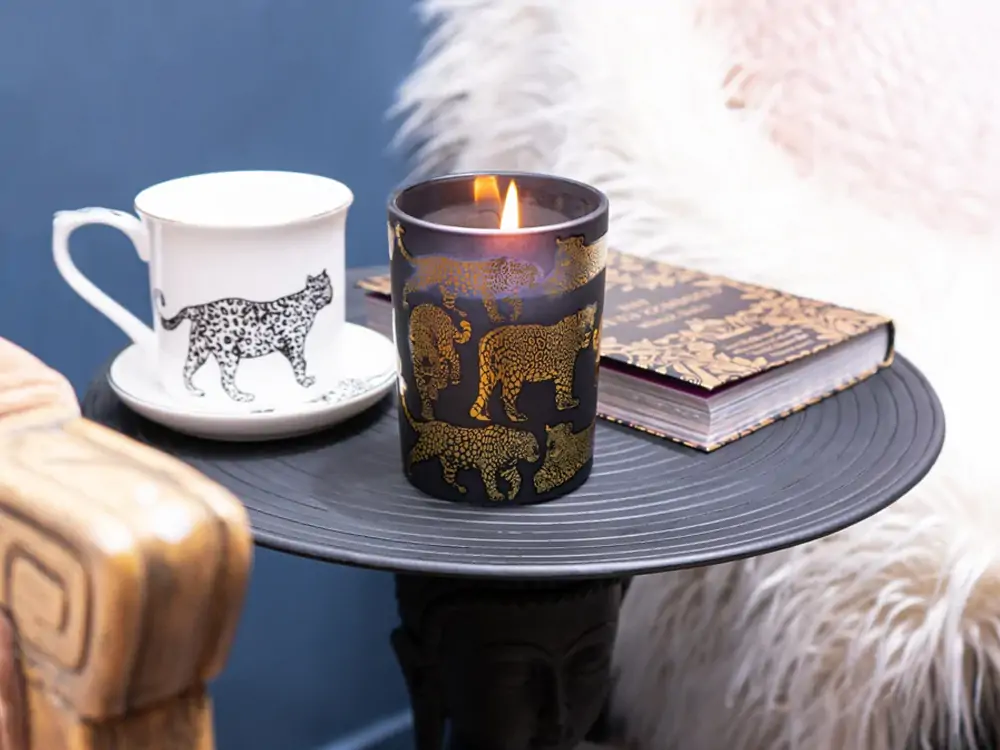
In this article, we will dive into the specifics of rotary printing. This post will cover the technique’s history, working principle, and application. It will also explore the types, benefits, and cons of rotary printing. By the end of this article, you’ll see just how essential it is in modern manufacturing and design.
History of Rotary Printing
The history of rotary printing can be traced back to the early 19th century. In 1843, American inventor Richard March Hoe created the first rotary printing press.
Before his invention, the traditional printing presses of those times were slow and hard to use. They were flatbed presses with an even older history dating back to the 15th century. As a basic printing process, there was a limit to how fast or how much a flatbed press could print.
Therefore, when Richard Hoe created a rotary printing press that was not only fast, but efficient. It served as a revolution in the printing industry. Richard’s creation used a rotating cylinder to apply ink to paper at a continuous pace. This, by no doubt, quickened the process and increased output.
The impact of the rotary press was most pronounced in the newspaper industry as it enabled mass production of newspapers in little time. This milestone set the stage and is the foundation for modern printing as we know it.
Working Principle of Rotary Printing
The working mechanism of rotary printing involves using a rotating cylindrical plate to transfer ink onto a surface. The main part of a rotary press is the printing cylinder. This component is usually metal with pre-engraved texts or designs. These designs or texts depend on the printing method, which we’ll discuss soon. Ink is applied to the printing cylinder to engrave text onto the material.
After this, the material to be printed is fed to the press. The printing material could be paper, plastic, or fabric and moves between two cylinders. One cylinder applies the ink while the other presses the material to secure the ink.
After securing the ink on its surface, the material or substrate will go through a drying process. This drying step may involve UV light, heat, or air drying. Afterward, the handler collects the printed material. Which might undergo extra steps like folding, cutting, or laminating.
Types of Rotary Printing
There are several types of rotary printing. They include offset lithography, letterpress, flexography, and rotogravure printing. Each method has its unique features and uses and this section will reveal all you need to know about them.
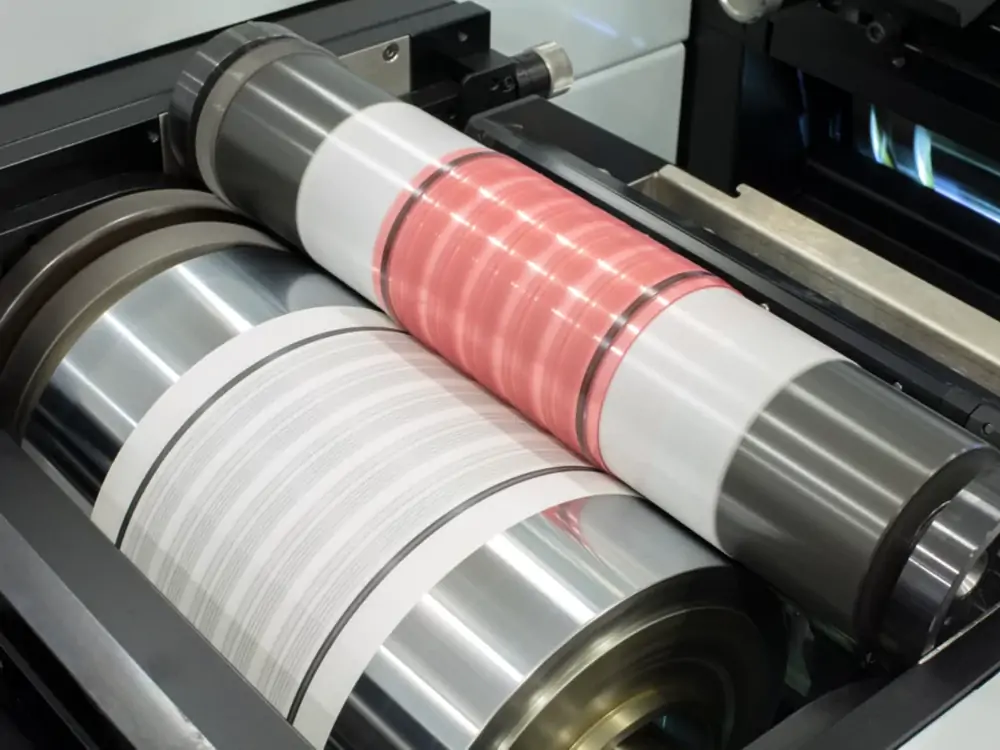
1. Rotogravure (Gravure) Printing
Often referred to as gravure, Rotogravure printing is a high-quality and quantity printing process. It involves engraving images onto a cylindrical plate using a laser, diamond stylus, or other mechanical means.
The engraved areas of the plate are called cells and are placed below the cylinder’s surface. Before engraving, a layer of copper is applied to the steel cylinder. Afterward, the cylinder receives a coat of chrome to increase its durability.
The next step involves covering the entire cylinder surface with ink that fills the cells. After that, a blade wipes the surface of the cylinder to remove ink from the non-image areas while leaving ink in the cells.
The gravure process continues with the inked cylinder pressing against the substrate. It presses the material with a rubber-covered impression roller, which allows the substrate to pick up the ink from the cells.
This transfer moves the image onto the substrate before it passes through a drying section to set the ink.
Rotogravure printing produces sharp images with rich and consistent colors. Gravure printers are also quick and durable. Their speed makes them suitable for applications that require large-volume production. This feature makes them a common choice for magazine, wallpaper, and packaging industries.
Additionally, they can resist millions of impressions before needing replacements. This favor makes them suitable for long print runs.
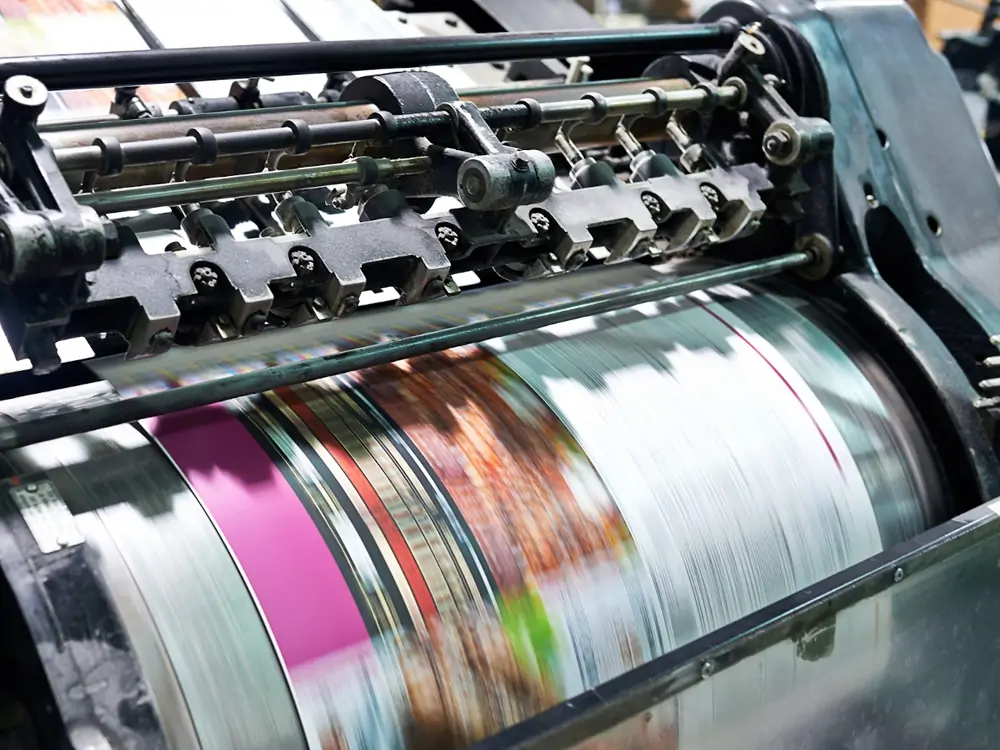
2. Offset Lithography (Offset printing)
The offset printing process uses three cylindrical components. These include a plate cylinder, a blanket cylinder, and an impression cylinder.
The plate cylinder is usually made from aluminum. It uses the principle of oil being hydrophobic to attract and repel ink to and from the image and non-image areas.
As the plate cylinder rotates, it gets soaked with water, which covers the non-image areas. It then picks up the oil-based ink from the inking rollers and places it on the image areas. The inked image then transfers to a rubber blanket cylinder that revolves against the plate cylinder.
Afterward, the inked image moves from the blanket cylinder to the impression cylinder. It is this impression cylinder that has the printing surface wrapped around it.
As the cylinders remain in constant motion, it allows for quick printing of thousands of impressions per hour.
This makes offset rotary printing ideal for producing sharp texts and images on different substrates. Applications of offset printing include the mass production of books, newspapers, and magazines.
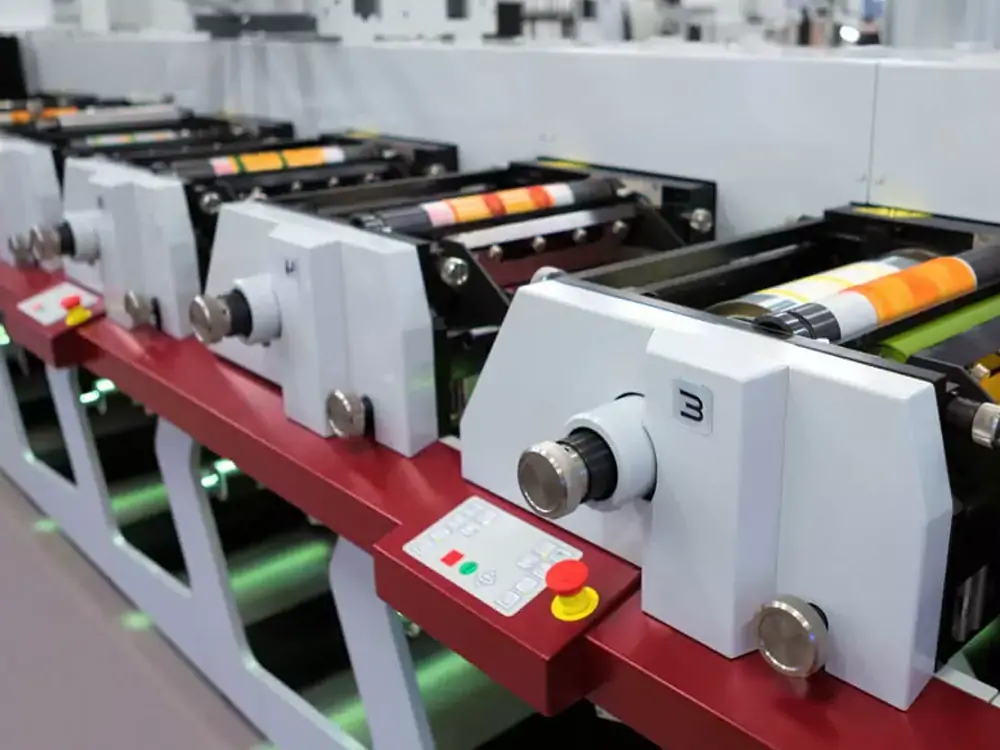
3. Flexography (Flexo) Rotary Printing
Flexography uses a flexible relief plate wrapped around a rotating cylindrical printing form. The resulting image from this process is raised on the plate surface.
In flexo printing, as the plate cylinder rotates, it carries ink from a roller with a finely engraved cell pattern. The raised image areas on the plate then transfer the ink directly onto the printing surface. This printing surface could be plastic, cellophane, metallic films, and paper. The flexible plates bend around the cylinder for flexographic printing on various surfaces.
This printing method works best for flexible packaging materials. Some of these materials include labels, pouches, and bags.
An important aspect of flexo printing is its adherence to food safety requirements. It produces quality prints that are cost-effective for packaging print runs.
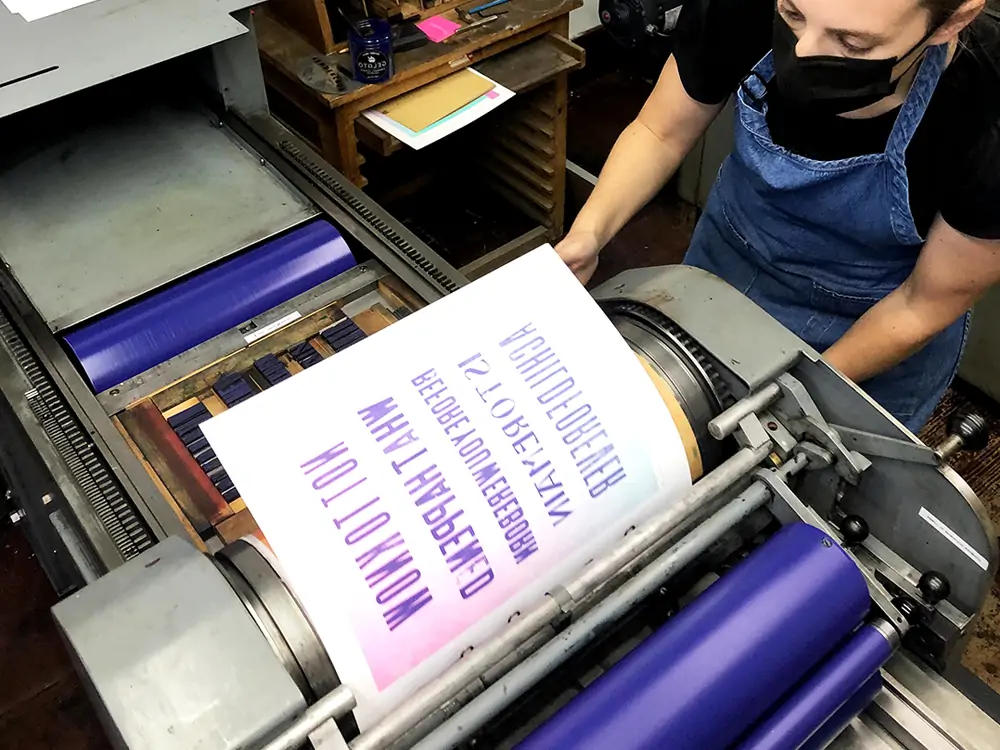
4. Letterpress Printing
This is one of the oldest and most traditional forms of rotary printing. Letterpress printing involves using a revolving cylindrical plate or drum with raised images or texts.
This method has a long history and was used for printing books and publications. That is, before the emergence of modern printing techniques.
One of the advantages of letterpress printing is that it creates a vivid impression on the printed material. This makes it a favorite for applications involving stationary, invitations, and artistic prints.
Although letterpress printing has little influence over other printing methods, it is valuable. This printing method remains a common choice for fine art, small-batch, and other aesthetic printing.
Advantages of Rotary Printing
- Efficiency:
Rotary presses operate at high speeds. They maintain constant rotation and thus allow for uninterrupted printing. This makes them efficient and suitable for large print runs and mass production. - Versatility:
Different rotary printing methods support printing on various materials. These materials include paper, metals, plastics, bags, cardboard cartons, and textiles. - Cost-effective:
Rotary printing is more cost-effective for long print runs than other methods. This is due to its efficiency and low material waste during printing. - Consistency:
The cylindrical foundation of a rotary printing press ensures consistent ink spread. It also assures there is uniform print quality during the entire print run. - Automation:
Modern printing presses are fully automated. This unique feature reduces labor costs and boosts productivity.
Disadvantages of Rotary Printing Press
- High initial costs:
While they have many benefits, rotary presses also have drawbacks. An example of this is their high initial cost. Rotary printing presses are large complex machines that require a heavy investment. This makes them unsuitable for applications or small businesses with limited budgets. - Setup time and costs:
Preparing rotary printing plates or cylinders is expensive and time-consuming. This is especially so for jobs that need constant changes or small prints. - Complexity:
As we mentioned earlier, rotary presses are complex machines. This means they require skilled handlers and maintenance personnel to operate them. As a result, there will be an increase in operational costs. - Registration issues:
This is a challenge in high-speed printing on fabrics or materials prone to moving during the process. In rotary printing, registration is the precise alignment of different colors of the printed image.
We say there is proper registration when the various components of the design are in the correct position and alignment. The result of this is a clear and balanced final print.
When printing at high speeds, there’s a chance that the substrate will face distortion and skewing. A situation where any of these happens will cause the different colors of the printed design to go out of register. - Color Limitations:
There is a limit to the number of colors a rotary press can create per print. The highest quality printing press can only produce 16 colors per print due to the practical limitations of the process. As the number of colors increases, the complexity of printing grows. It would need more screens, precise registration, and longer setup times.