Screen printing relies heavily on mesh counts to determine print quality. Mesh count, indicating the number of threads per inch in the screen fabric, plays a pivotal role in achieving clarity and precision. The choice of mesh count is not random. It requires careful consideration of multiple factors to achieve the best results. Each mesh count has specific benefits and difficulties, and we need to grasp these nuances.
We analyze different mesh counts to understand their strengths and limitations. From coarse to fine meshes, each type offers distinct opportunities and considerations. Addressing mesh count misconceptions boosts clarity in screen printing. This way fosters confidence in navigating this critical process. This article strives to be a valuable resource for both newbies and seasoned professionals. In this article, we will explore screen printing mesh counts to equip readers with understanding.
Join us as we unravel the mysteries of screen-printing mesh counts on this journey toward elevated craftsmanship.
Let’s Go!
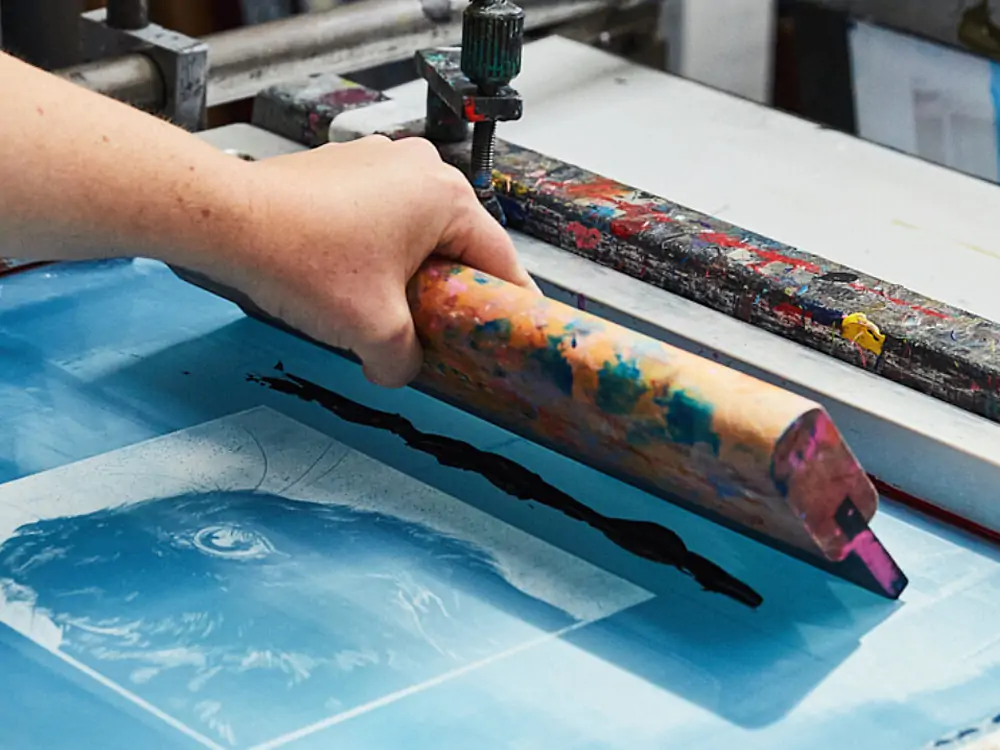
Basics Of Mesh Counts
Mesh count refers to the number of threads per inch or per centimeter in a screen-printing mesh. It represents the density of the mesh fabric, indicating how many threads are woven into a given area of the mesh. Screen printing uses a stretched mesh over a frame to transfer ink onto paper, fabric, or wood to create images.
Mesh count determines print quality, detail, and accuracy in screen printing. It varies for different applications based on design, substrate, and ink. Higher mesh counts have finer openings for intricate designs and details. On the other hand, lower mesh counts have larger openings for bold designs or heavier ink deposits.
Understanding mesh counts is essential for achieving desired results in screen printing. Printers must choose the right mesh count for each project. This step will ensure high-quality prints. Mesh count affects clarity and durability.
Common Types of Mesh Counts
Here are some common types of mesh counts for printing
1. Low Mesh Counts:
- Thread Count: Typically ranges from 15 to 77 threads per inch (6 to 30 threads per centimeter).
- Characteristics: Low mesh counts have larger openings between threads, allowing for heavier ink deposits. They are suitable for printing on coarse materials like heavy textiles, canvas, or wood.
- Applications: Ideal for printing bold designs, solid colors, or where a thick ink deposit is desired. Commonly used in applications like posters, signage, banners, and printing on substrates needing a thick ink layer.
2. Medium Mesh Counts:
- Thread Count: It usually falls between 80 and 180 threads per inch (32 to 71 threads per centimeter).
- Characteristics: Medium mesh counts offer a balance between ink deposit and detail. Versatile, they are commonly used for general printing on fabrics, paper, cardboard, and other substrates.
- Applications: Medium mesh counts support a wide range of designs, including graphics, text, and images. It is commonly used in apparel, packaging, promotional, and other commercial printing applications.
3. High Mesh Counts:
- Thread Count: Ranges from 200 to 420 threads per inch (79 to 165 threads per centimeter).
- Characteristics: High mesh counts have finer openings between threads. This mesh count allows for precise detail reproduction and smoother ink deposition. They offer superior resolution and are ideal for intricate designs.
- Applications: Ideal for printing intricate details and small text on delicate materials like paper, fabric, or electronics. It is commonly used in applications where high-quality prints with refined details are essential. Such as fine art printing, textiles, electronics, and circuit board printing.
Note: Understand the characteristics and applications of each mesh count type. Select the proper mesh count for your printing project. Testing is necessary to find the best mesh count for desired results. Experimentation may be needed.
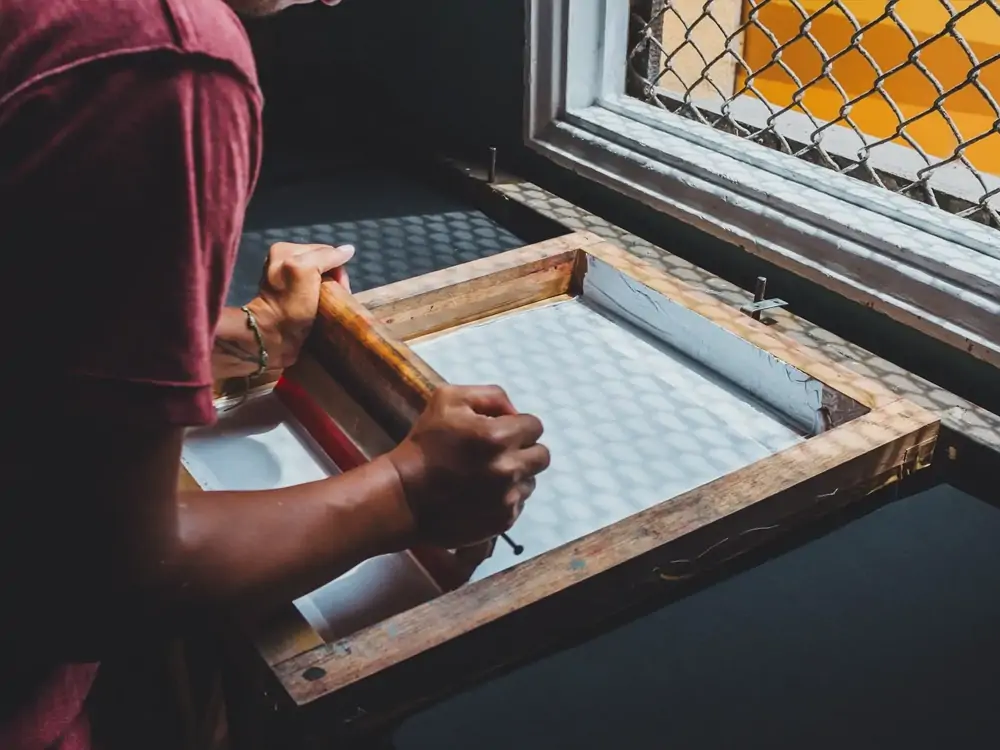
Why Mesh Counts are Important?
Mesh counts are essential in screen printing for several reasons:
- Detail and Resolution: Mesh counts determine the level of detail and resolution achievable in prints. Higher mesh counts result in finer thread openings for detailed design reproduction. This enables accurate replication of intricate designs and fine details. Lower mesh counts are suitable for bold designs but may lack detail.
- Ink Deposition: Mesh counts influence ink deposition and thickness. Finer meshes hold less ink. They produce thinner layers, perfect for printing on delicate substrates. Lower mesh counts allow for a higher volume of ink deposition, which is suitable for thicker materials.
- Print Quality and Durability: Choosing the right mesh count prevents ink bleeding and smudging. Doing this step will ensure clean prints. And it enhances print longevity with good ink adhesion and durability.
- Efficiency: Mesh counts affect the printing speed and efficiency. Higher mesh counts need more time and precision for finer details. Lower mesh counts enable faster printing but may sacrifice detail. Understanding this relationship helps printers optimize their production process while maintaining print quality.
- Versatility: Different mesh counts cater to various applications and substrates. Printers can achieve optimal results by selecting the correct mesh count for each project. This customization ensures the best outcome for their needs.
P.S. Mesh counts are important in screen printing. They affect detail, ink deposition, print quality, durability, and printing efficiency. Printers can make informed decisions and achieve consistent results by understanding mesh counts.
How to Choose Suitable Screen Mesh Counts: Eligibility Criteria
Choosing the right mesh count is crucial for achieving optimal results in screen printing.
Here’s a guide on how to select the appropriate mesh count for your printing needs:
- Consider Design Complexity: Evaluate the level of detail and intricacy in your design. Fine details require higher mesh counts, typically ranging from 200 to 305 threads per inch (79 to 120 threads per centimeter). Simpler designs with bold elements may need lower mesh counts. These range from 110 to 160 threads per inch (43 to 63 threads per centimeter).
- Assess Substrate Type: Determine the material you’ll be printing on. Thicker materials like textiles or wood need lower mesh counts. This allows for better ink penetration and coverage. Higher mesh counts are better for thinner substrates like paper or fabric to achieve finer details without ink bleed.
- Ink Deposit Needs: Consider the desired thickness of the ink deposit. Finer meshes hold less ink. They produce thinner layers, suitable for precise details. Lower mesh counts allow heavier ink deposition, perfect for bold, vibrant designs.
- Perform Test Prints: Conduct test prints using different mesh counts to observe how they affect the final result. This experiment will determine the mesh count for your design, substrate, and ink.
- Consult with Suppliers or Experts: Consider factors and conduct test prints to confidently select the best mesh count for high-quality screen printing. Choose the count that will ensure accurate prints for your projects.
If unsure, seek advice from screen printing suppliers or experienced professionals. They offer valuable insights and recommendations from their printing expertise. They know various printing scenarios.
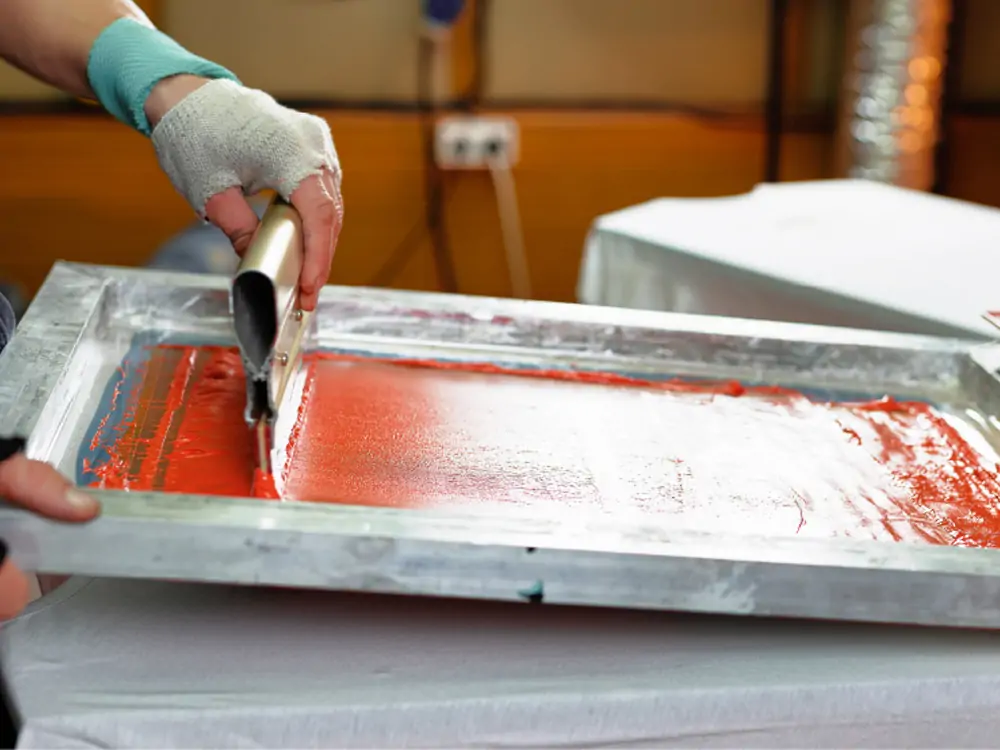
Drawback of Inappropriate Mesh for Screen-Printing
Inappropriate mesh counts can harm screen-printed products. This leads to wasted resources and customer dissatisfaction. Therefore, Printers must consider the mesh about design, substrate, ink type, and desired print outcome for best results.
- Loss of Detail: If the mesh count is too low for the design’s complexity, fine details may be lost or appear blurred in the print.
- Ink Bleeding: Using a high mesh count with the wrong ink or substrate can cause the ink to bleed or spread beyond the design boundaries, resulting in blurred images.
- Ink Buildup: A low mesh count with high ink viscosity leads to excess ink on the substrate, causing smudging, smearing, or uneven coverage.
- Ink Starvation: Conversely, using a mesh count that is too high for the ink viscosity may lead to ink starvation. The ink does not flow smoothly through the mesh. This results in patchy or inconsistent prints.
- Poor Adhesion: Inappropriate mesh counts can also affect ink adhesion to the substrate. If the mesh count is too high, the ink may not penetrate the substrate adequately, leading to poor adhesion and durability of the print.
- Print Quality Issues: Incorrect mesh count can cause print quality issues like uneven ink, color distortion, or texture loss.
- Waste of Resources: Using the wrong mesh counts in printing wastes materials like ink, substrates, and time. Prints might need redoing to achieve the desired results.
- Reduced Efficiency: Inefficient mesh counts can slow down the printing process. It leads to decreased productivity and increased production costs.
Final Verdict
Mesh counts are crucial for high-quality screen printing. Understanding their significance is essential. The mesh count directly affects detail level, ink deposition, print durability, and efficiency. Printers can ensure faithful prints by selecting the right mesh count. If the choice depends on design intricacy, substrate type, and desired print outcome. Then, sharpness, clarity, and durability are guaranteed.
Using the correct mesh count reduces printing problems like ink bleeding, poor adhesion, or detail loss. This results in efficient production and happy customers. Meticulously consider mesh counts for best screen-printed quality. This is crucial for various industries.