Custom shot glasses have gained popularity in the promotional merchandise and souvenir industries.
As demand increases, customers are expecting more. To meet the market expectations, manufacturers need to build custom shot glasses with durability, precision, and consistency.
High-quality prints are expected from customers that won’t scratch or fade. That is why glass printing, especially in bulk, requires reliable technology.
In today’s competitive market, the print on glass opportunity gives you a clear edge.
In 2024, the global glass drinkware market was valued at approximately USD 13.95 billion. It includes items like shot glasses that are printed and decorated. By 2030, experts predict it will have grown to USD 26.09 billion. Between 2025 and 2030, the market is projected to expand at a compound annual growth rate (CAGR) of 11.1%.
In hospitality and retail, this surge is driven by the rising popularity of customized items.
In this guide, you will learn how to screen print shot glasses the exact way. We will guide you through printing processes, ROI considerations, and machine specifications. So you can determine which screen printing machine is best for your needs. Let’s begin.
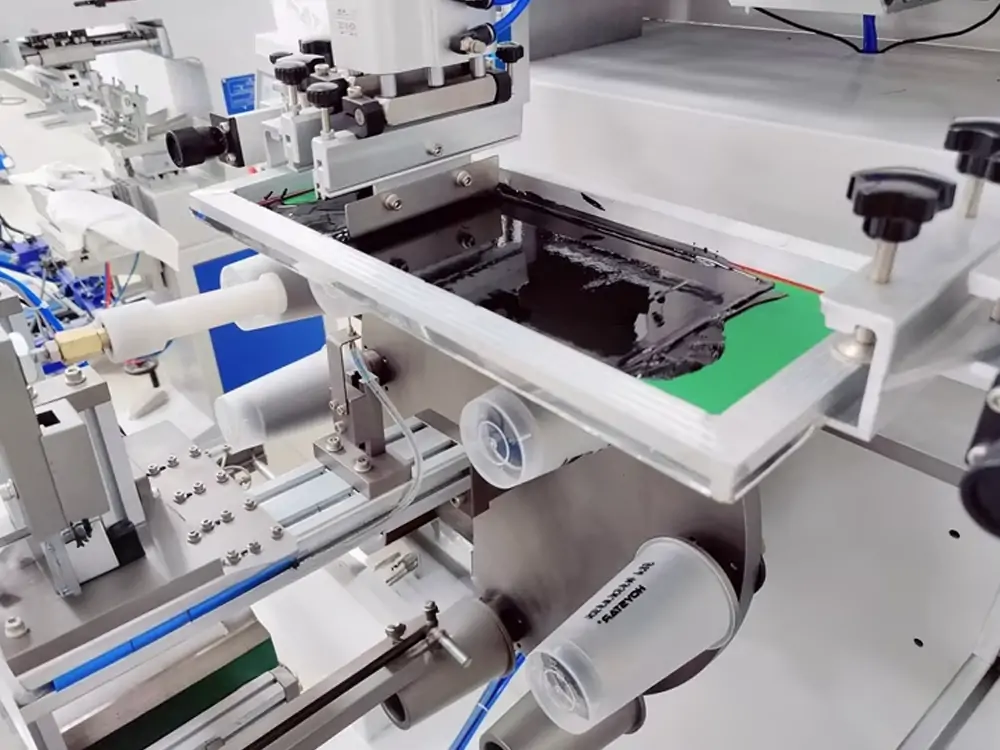
Shot Glass Screen Printing
What is Screen Printing?
It is a technique in which ink goes through a fine mesh stencil (screen) onto a surface. To push the ink through the screen, you have to use a squeegee. This will create long-lasting & bold designs.
When you print on glass, the results are excellent. Why? Because it provides strong ink adhesion. The result? Your print remains bright, bold, and it doesn’t fade. It’s also resistant to dishwashing & scratching. So, if you need custom shot glasses that are long-lasting, screen printing is a great choice.
A clean and precise method is required when printing on glass. Screen printing covers all the needs.
How It Applies to Shot Glasses
Printing on shot glasses may seem like a small task, but it’s not that simple. They are cone-shaped and curved. These shapes create a challenge.
Compared to a flat surface, you can’t simply print that way. A design is required that smoothly wraps around the glass. It’s where precision is required. One wrong step, and your print looks blurry and crooked.
Comparison of curved & flat is here:
Feature | Flat Surface Printing | Cylindrical Object Printing |
---|---|---|
Method of Print | Flatbed press | Semi-automatic or Rotary |
Registration needs | Moderate | High (due to curvature) |
Complexity Setup | Lower | Higher |
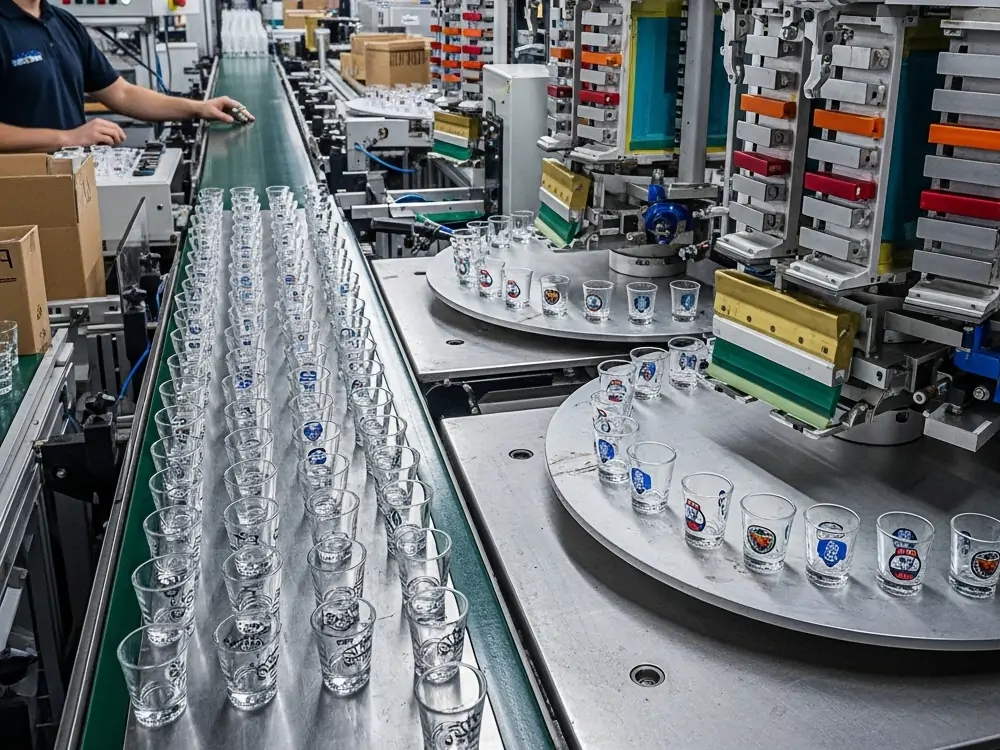
Key Machine Types & Configurations
It’s essential to understand the various key machine types available when selecting a shot glass screen printing machine. Each offers efficiency, different speeds, and operational control, depending on the needs of your production. Three of the most common machines are given below:
Manual Machines
These machines are ideal for small-scale operations. They require full operator control, from pulling the squeegee to shooting the glass.
They are best suited for prototyping, custom designs, or short production runs. However, their limited production capacity remains due to the hands-on process despite the low investment. Operators must align each glass precisely, making the process labor-intensive and time-consuming.
Semi-Automatic Machines
These machines offer a middle ground. The machine controls the printing cycle while loading & unloading the custom shot glasses.
It will give you better consistency & speed. It’s great when you are growing your business and want to print on glass. Small manufacturers prefer this for medium production runs.
Fully Automatic Machines
For serious volume, these machines are the preferred choice. They feature unloading, printing, alignment, and automatic loading. With minimal labor, you can continuously screen print shot glasses.
If you run a factory or handle OEM orders, this is your go-to solution. It offers great precision with high output.
Machine Type | Print speed (pcs/hr) | Operator Needs | Typical Use Case |
---|---|---|---|
Manual | 50-150 | 1-2 | Short runs, Custom designs |
Semi-Automatic | 200-500 | 1 | Medium-scale output |
Automatic | 600-1200+ | Minimal | OEM orders, Large factories |
The right machine will help you generate cleaner, faster, and more consistent custom shot glasses without compromising on print quality.
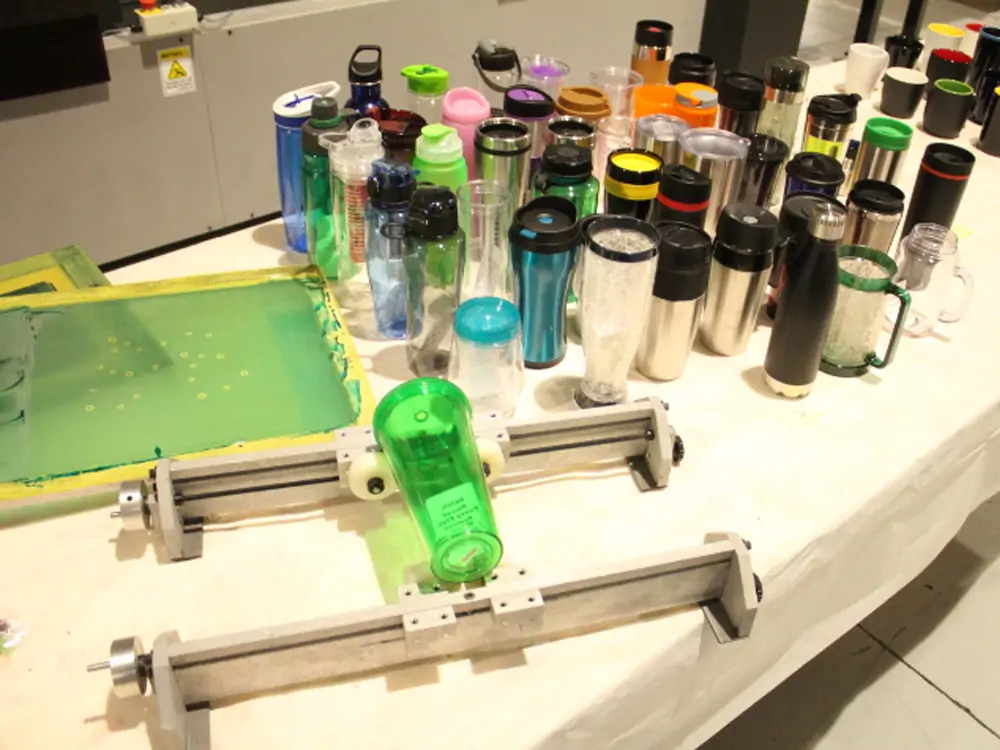
Technical Specifications to Evaluate
When selecting a shot glass screen printing machine, look beyond basic features. Right can help you reduce errors, deliver high-quality results, or print faster. Whether you are upgrading your setup, these are the most technical specifications to see.
Print Speed & Throughput
The speed of print is measured in pieces per hour (pph). It directly affects how many custom shot glasses can be produced each day.
There are several factors affecting speed:
- Number of print stations
- Drying method (UV tunnel or infrared)
- Type of ink used (Thermoset or UV)
If you plan to print on glass for high-volume orders, consider a machine with fast-curing technology and multiple stations.
Print Area & Glass Size Range
The size of the shot glasses you plan to print on your machine must be supported by it. Many machines handle a diameter range of 20-80 mm and different height levels.
This is crucial if you want to expand your product line or offer different glass styles.
Registration Accuracy
If the registration accuracy is high, it ensures clean and aligned prints, particularly for different color designs. Machines with a tolerance of 0.2 mm are preferable.
Squeegee Pressure & Stroke Control
If the pressure of the squeegee is controlled, it will ensure an even distribution of ink. With adjustable pressure settings, the machine will produce sharper and cleaner designs.
Unlike basic pneumatic systems, servo motor-driven systems offer greater control, which makes them ideal for custom shot glasses with detailed prints.
Ink Compatibility
All ink type is not supported by all machines. UV-curable inks are durable and fast-drying. These are perfect for printing on glass applications.
Your machine should include a UV tunnel or infrared drying system that will match the ink you have chosen.
Changeover Time & Ease
If you work with multiple clients or print various designs, quick changeover is essential. Look for:
- Modular screens
- Easy cleaning access
- Modular screens
It will save you time, and your workflow will be smooth.
Quick Summary of Key Specs:
- Registration accuracy
- Print speed
- Curvature support
- Ease of maintenance and cleaning
- Max/min diameter
By keeping these specs in mind, you will choose a machine that delivers custom shot glass prints and meets your needs.
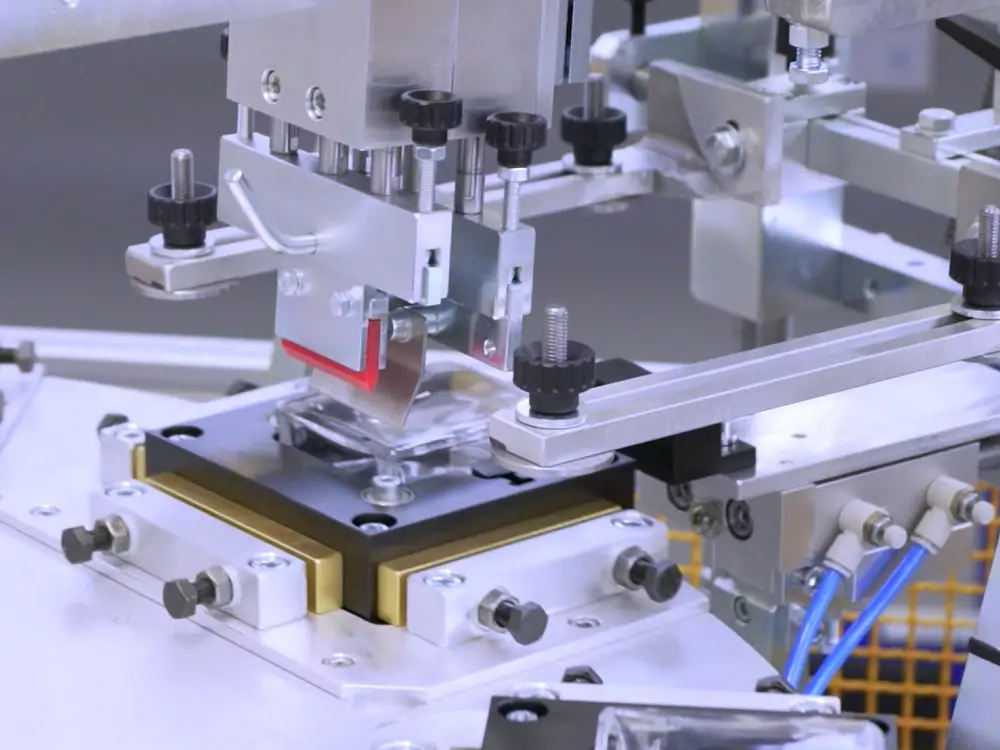
Production Workflow & Integration
To efficiently produce machine-custom shot glass printing, a smooth production workflow is crucial. At scale, when deciding how to screen print shot glasses, machine integration and automation play a significant role in quality, consistency, and speed.
Feeding & Loading Options
These systems have an impact overall. Manual loading slows down production, but it is suitable for short runs.
Glass orientation is also important. Before printing, an automated system aligns each shot glass correctly. It will prevent misprints and ensure consistent results are driven, especially when printing is done on glass with curved surfaces.
Curing & Drying
It solidifies the ink. Machines may include a separate conveyor tunnel or an integrated UV curing unit.
Quality Control
Modern machines support built-in quality checks. Vision systems for custom shot glasses detect defects such as smudges or misalignment.
Some machines integrate with ERP or MES systems for advanced traceability. It helps to track data and maintain quality across orders.
Total Cost of Ownership
It’s essential to consider the total cost when selecting a shot glass screen printing machine. Buyers who are technically focused on long-term ROI, which balances performance with operating costs. When producing custom shot glasses at scale, it’s a necessity.
CapEx vs. OpEx
- Capital Expenditures (CapEx) include the initial setup, installation, and purchase of machines. These are one-time costs.
- Operating Expenses (OpEx): It covers the day-to-day running costs. Which includes screens, inks, energy use, and routine maintenance. If not managed carefully, operating expenses (OpEx) can exceed capital expenses (CapEx).
Energy Consumption
The energy usage of the drying system varies.
- Infrared (IR) curing. It typically requires more space and consumes more power.
- UV curing systems consume less energy per unit, making them cost-effective for continuous operations.
If you aim to print on glass effectively for businesses, these energy savings can significantly boost your profit margins.
Downtime & Maintenance
Unexpected downtime hurts productivity. Select machines that come with readily available spare parts and local support.
Also, consider the Mean Time to Repair, which is the lower, the better.
Cost Component | Typing Annual Cost | Notes |
---|---|---|
Consumables & Ink | $3000-$7000 | Varies by design coverage & by volume |
Utilities | $2000-$5000 | Depends on the hours used and the drying method |
Maintenance | $1500-$4000 | Based on wear & service intervals |
Advanced Features & Future-Proofing
Choosing future-ready machines gives you a clear advantage as demand for custom shot glasses increases. Suppose you are interested in how to learn and scale screen-printed shot glasses. Then, advanced features can boost speed, sustainability, and quality.
Servo Motor Control
Higher precision and programmable stroke are controlled by machines with servo motor control, particularly printing when you have to print on glass with conical or curved surfaces.
IoT & Data Logging
IoT integration is mostly installed in modern machines. This allows real-time monitoring of ink usage, system performance, and print cycles. For preventive maintenance, you will receive automatic alerts that help reduce repair costs and prevent downtime.
Modular Design
Your capabilities are expanded by using a modular setup. With basic single-color printing, start with this first, then add stations for foil stamping, multi-color jobs, or even laser printing. This flexibility will help you grow without changing the entire machine.
Eco-Friendly Option
Sustainability is the key. New machines support low-VOC inks, which reduce harmful emissions. UV LED curing systems can also be chosen, which will use less energy and last longer than traditional UV lamps.
Comparing Brands & Suppliers
It’s not just about features when choosing the right shot glass screen printing machine. It also depends on who you are buying from. You need a reliable supplier to consistently produce high-quality custom shot glasses.
What to Look For
First, check the country where it is manufactured. Machines made in Japan, Germany, or the USA offer better build quality and precision. At the same time, consider import taxes, shipping times, or service availability.
Local support and operator training make sure that the supplier offers it. If the team is responsive, then it reduces downtime and helps you get the most from your investment. Also, see the warranty coverage. Look for coverage, technical support, and 12-24 months.
Requesting Samples & Demos
Ask for a sample print before you decide. Send your authentic shot glasses and, by using your specific design request, request a demo.
Test for scratch resistance, clarity, and adhesion. It will help you evaluate real-world results, especially when you are switching to a machine or learning how to screen print shot glasses.
Questions to Ask Before Buying
What is the max/min diameter & height supported?
For custom shot glasses, most machines support diameters from 20-80mm and heights of 120mm.
Average changeover time?
It is ideal for multi-design production. Quick-change allows changeovers in 10-20 minutes.
Is registration servo-controlled?
Yes, for precise registration and consistent glass alignment, servo motors are used by high-end models.
Type of inks supported and curing method?
Machines support thermoset inks and UV-curable inks with infrared curing systems.
Warranty & local service availability?
12-24 months standard warranty range.
Typical throughput in real conditions?
Automatic ones print 600-1200+, while semi-automatic ones print 200-500 pieces per hour.
Can a machine handle conical vs. straight glasses?
Yes, rotary screen printers can print on both conical and straight custom shot glasses.
Availability of spare parts?
Top suppliers offer local stock and fast shipping for components and critical spare parts.
Conclusion
Right shot glass printing while choosing it’s more than a price decision. You must evaluate workflow integration, technical specs, and total cost of ownership. These factors directly impact your efficiency, print quality, and long-term ROI.
When a well-matched machine helps you, it helps with speed and durability while printing on glass. It also lessens the downtime and saves energy. And support different custom shot glass designs. That’s why understanding features like ink compatibility, servo control, and changeover time is essential.
Before buying, request test prints and demos using your glassware. Talk to users who are already using it to see how it works in real production.
In the end, the right choice ensures higher-quality prints, smoother operations, and faster returns on your investment. Don’t adjust. Print smarter & invest smarter.
Ready to elevate your brand? Start printing high-quality custom shot glasses today!