Screen printing is the printing technique most frequently employed on an industrial level. This printing method uses A woven mesh to hold up an ink-blocking stencil. Pressing the connected pattern through the mesh leaves open spaces that can be filled with ink or other printing materials. The image is then pressed through the mesh and onto a base. Moving a roller or squeegee across the screen image forces or draws ink material to the weaving mesh threads in the open spaces. This type of printing has become much more popular recently because it can be used for many different things and because rotary screen printing tools can make many things at once.
Main Types of Screen Printing
Rotary and flatbed screen printing are the two main types of screen printing. You can either print on a flatbed screen by hand or automatically. Most of the time, rotary screen printing is automatic and produces the most prints per hour. For screen printing, the print material is put on the cloth by running it through a net or screen with some open and some closed areas, depending on the pattern you want to make. The print design on the fabric is based on the pattern of the screen’s empty spaces.
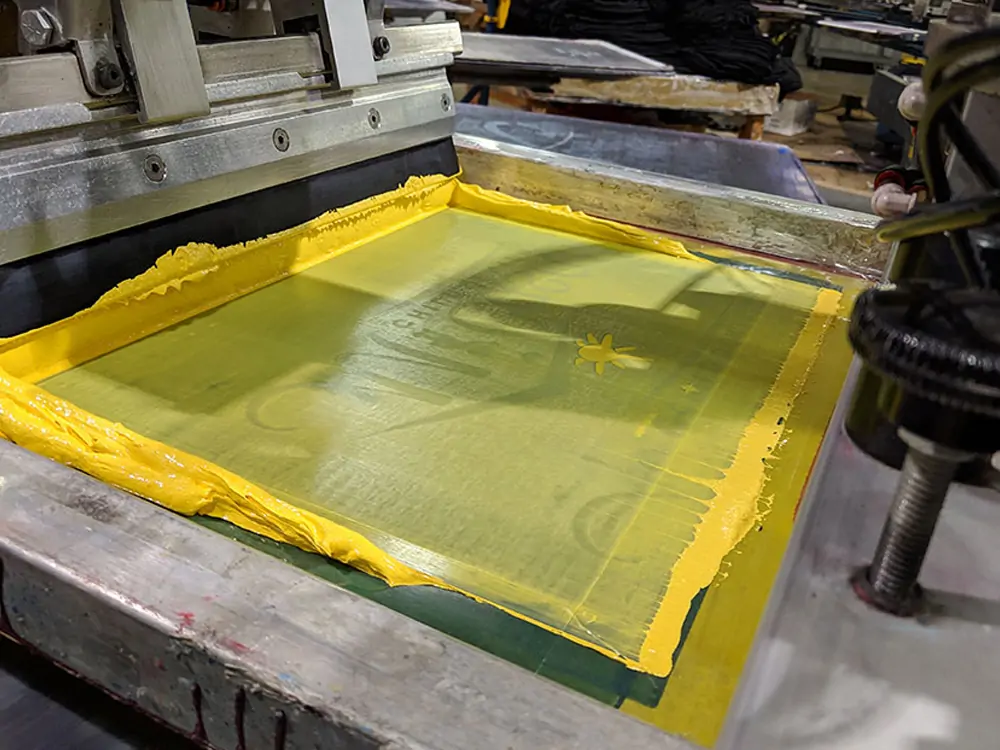
Difference Between Rotary Screen Printing and Flat Screen Printing
• Printing High Volumes and Reproducibility
Mass production is necessary for some applications, such as printed circuit boards. Reproducibility and high-volume printing are crucial for this kind of mass manufacturing.
These two aspects are the most compelling reasons for rotary screen printing for Printed Electronics and Industrial Printing. Rotary screen printing, as the name implies, is a continuous process that lasts longer than other screen printing methods. This enables the print line to consistently produce goods, thereby facilitating the production of greater volumes.
If your application requires the production of large quantities of components that need to be consistently reproduced, a rotary screen printing technique is often the most appropriate and effective option.
• Combining for Different Purposes
Lastly, many businesses care a lot about how well it works with their current print line. However, printing in large quantities is where rotary screen printing shines. It can be used for other things as well. When compared to flatbed screen printing, rotor screen printing is simple to set up.
Additionally, the system permits printing brief batches, allowing for testing printing processes during the integration phase. Rotary screen printing is great for testing and study because it can be done at low speeds.
• Screen Lifespan
An additional factor that can result in long-term cost savings is the lifespan of equipment. One often-stated benefit of rotary screen printing is that screens last long. Even though rotary screen printing costs more to set up and has less downtime, the screens last longer and cost less in the long run because they don’t need to be replaced as often.
Screens with an extended lifespan can be rationally replaced more frequently. This cuts down on machine downtime, which saves money over time. So, deciding how long the screen printing will last is crucial when choosing a method for your Industrial Printing line.
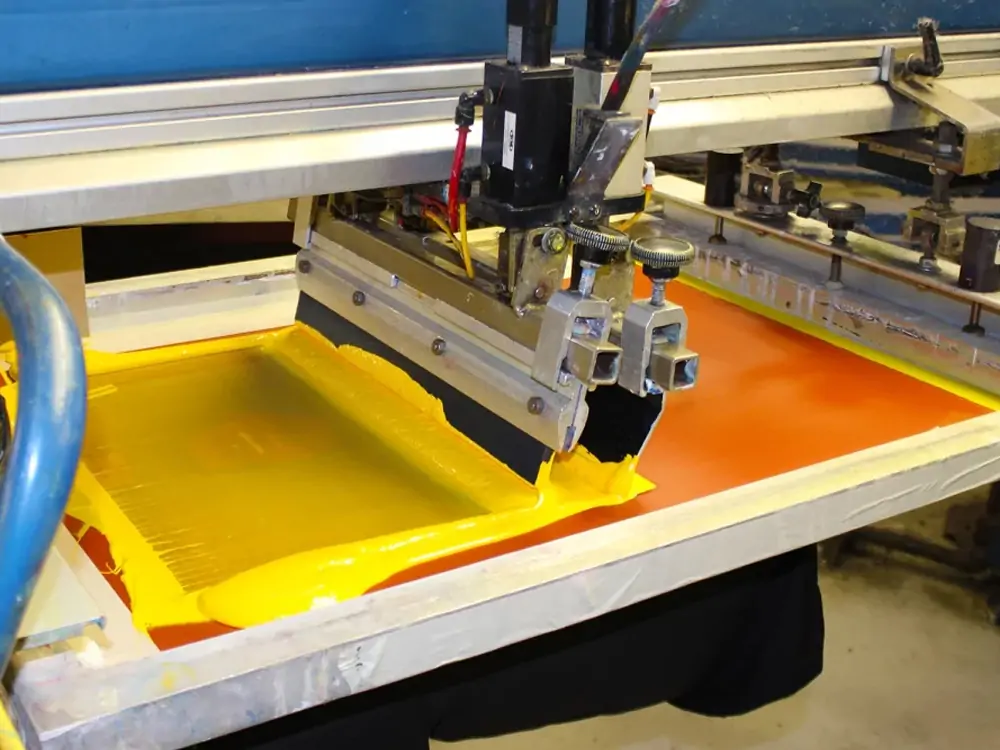
• Pace of Printing and Continuity
One key distinction is the change rate, which continuity affects. Printing with a flatbed screen requires two strokes. To begin, ink is spread across the screen to fill the mesh’s holes. The term preferred for this is prefilling. When the squeegee hits the base a second time, it forces the ink through the screen. This requires many passes of the squeegee for a single printout.
These same procedures are executed continuously in rotary screen printing. The mesh is prefilled without an additional stroke since the ink roll is ahead of the squeegee blade. The squeegee aims to force the ink past the screen and onto the substrate. Though integral to the ongoing procedure, it is unnecessary for its stroke.
Flatbed screen printing uses two meters for each step—one for prefilling and one for printing—but rotary screen printing only needs one meter. The ink rheology is improved due to the reduced real squeegee speed.
The inverse is also true: flatbed screen printers often employ a faster squeegee speed to handle bigger runs. On the other hand, the viscosity might increase if the ink travels rapidly. This causes variations in the printed output. Rotary screen printing allows for more consistent printing results with lower squeegee speeds while achieving the same or even faster output.
• Blockages of Printing Holes
Downtime and holes getting clogged are the main problems with screen printing methods. Clogged holes can change the outcome of printing, but they can also damage machines or screens permanently. Consequently, the frequently unanticipated expenses escalate another notch.
With rotary screen printing, the printing process is constant, even for prefilling, so the result is much more uniform than other screen printing methods. This is the case because the ink doesn’t build up on the sides of the machine. When you print on a flatbed, the ink often dries along the edges. After that, this gets on the screen and forms lumps that block the holes.
As was already said, this usually makes the writing worse. When using a flatbed for screen printing, check often to see if the ink has built up in places you didn’t expect it to. There may be an extra step in the process, but it could cost much more in the long run.
Difference Between Rotary Screen Printing and Flat Screen Printing: Final Thoughts
The kind of material you’re printing on, the amount of fabric you need to print, and your budget are some of the factors that will determine which of the two printing methods—flat-screen or rotary screen—would meet your requirements best.
As a precise and economical option, flat-screen printing is ideal for small to medium-sized print runs and designs using fewer colors. A quick and effective way to create high-quality, long-lasting prints, rotary screen printing is ideal for designs with more colors and greater print runs.